Ding Ding Round#2
After the van being in for an 70k ALL-IN service, they reported front pads & discs 75% worn.
more on that here:
@Dellmassive`s T6 T32 Sportline 204 LWB DSG PV MY18 - Van Adventure
and the awesome guys over at NUTEXA getting us sorted with a new set of fronts. . . Thanks
@Pauly &
@Nutexa Frictions
see here:
NUTEXA - Brake Pad & Disc change - How I Done It -
.
it was time to get it done. . . . remember last time we split the 21mm sockets on the front calliper bracket bolts. (so couldnt swap the discs)
so this time we have the new IMPACT rated socket set, the breaker bar and extension pole.
plus a new set of M16 21mm bolts (calliper bracket to hub) as according to the book the are stretch bolts and need replacing after removing.
.
starting off on the easier drivers side, id cracked the wheel bolts a half turn then jacked up the front.
I've used two jacks and two axle stands for this job. . . .
the jacks are on the jack points and the axle stands were fitted after on the sub frame.
also not forgetting to undo the brake fluid reservoir and place blue role around to catch any drips when the pistons get pushed back.
slider pins undone,
then piston pushed back using a pry bar against the pad and disk. . . . .
your see the calliper hanging on a calliper-hook to keep it safe and prevent the hose getting damaged.
this time i was ready for those tuff 21mm caliper bracket bolts. . . . id pre soaked them with WD40 already.
i tried the new IMPACT socket with the Nut gun - they didn't budge,
so it was time for the breaker bar + extension . . . . . they were very tight, but with a crack and a groan they come free. - sweet.
using the gun after that they come flying out.
now for the good stuff. . . . check out these NUTEXA discs and pads. . .
re assembly was simple enough. . .
clean everything with the wire brush.
new disc on, with spline keeper bolt + torqued to spec - see the pdf at the top of the tread. (TTS)
calliper bracket on with new 21mm M16 bolts ( purchased from the local TPS for almost £20 for the four! ) + TTS
pads in piston and on carrier.
small amount of appropriate grease on the slider pins and pad-calliper contact points
calliper on bracket and slider pins + TTS
while we are down here. . . . heres a quick look at the "CMS - crankshaft main seal," the van has just been in to VW as the sump seal was leaking( after them doing the CMS), so they have just redone it FOC.
the sump gasket is a type of silicone stuff.
Nice . . .
so its wheel back on, and move over to the other side. . .
+++++++++++++++++++++++++++
the other side is the same, except we have the pad sensor to deal with. . .
this part is damaged on this van - so i needed to repair the loom, but ill cover that in a different thread.
so same procedure to get to this point. . . . .
here's a closeup of those tuff bracket bolts while they are soaking in WD40.
this is with bracket and disc off, plus the pad sensor loom repaired. . . .
a quick rebuild - same as the other side we get to here . . . .
with the new pad sensor load - this time cable tied in to make sure it cant come out its mounting bracket
a final clean-up and have re fitted the calliper spring plate. . .
here is another look at the jack and stand positioning. . .
wheels back on, bolts TTS, and its back on the floor. . . .
here you can see why i didn't bother sorting out the red callipers - with these Dutchy rims you hardly see them, so i didn't bother touching up the paint.
maybe when i swap out to the Cantera's or Sportline alloys ill take another look at the painted pots
next up was to replace the brake fluid cap. . . no loss of fluid here as the level wasn't topped up as the pads wore down - so the level is now back to the MAX line.
now a few presses of the peddle to take up the slack till the peddle firms up.
now time for a gentle test drive. . .
the discs come with that sweet looking black protective coating, and the pads need seasoning / bedding in.
so its out for a local 5miles loop being very carful on the braking. . .
during the test drive with the window open there is a definate fluttering sound that the pads and discs are making - this is normal for the start of the drilled and vented discs.
after the test drive there is a small puff of smoke as the oils and paint coating get used to the hot temps. . .
cheaking all round you can see the pads bedding and wearing off the black coating. . . .
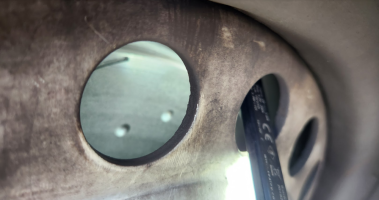
Pic Limit for this post. . .
so that it for now. . . the pads will need a while to bed in . .
so ill go easy for the next 100miles / 5days.
...
.
/
.